5S: Creating Efficiency, Order, and Excellence
At Fujicon, we have fully embraced the 5S methodology as part of our corporate culture, ensuring an organized, efficient, and safe work environment.
Description of 5S
5S is a Japanese management method that focuses on creating a cleaner, more organized, and more efficient work environment. This concept was first applied in the Toyota Production System (TPS) and has been proven to increase productivity and reduce waste in various industries.
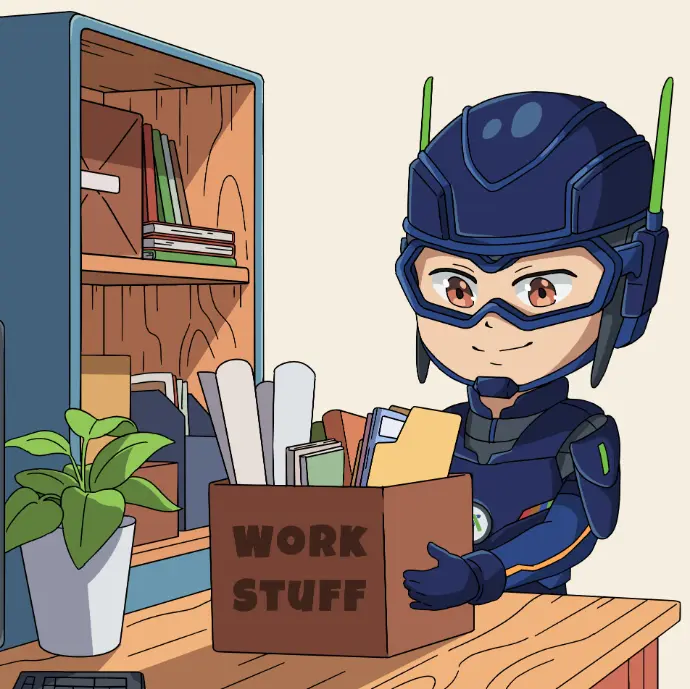
Seiri (Sorting)
Sorting Information and Digital Work Tools
In the consulting context, Seiri means sorting information, digital files, tools, and project resources to only those that are truly relevant and needed. For example:
- Deleting old, irrelevant project documents.
- Cleaning work folders and emails of spam or duplicate files.
- Sorting work tools (such as BIM software, IDEs, plugins, design templates) so that only those that are actually used are available.
🔍 Goal: Increase focus, work efficiency, and avoid confusion caused by too much information or unused applications.
Seiton (Organizing)
Structuring Work Systems and Processes
Once the information and tools have been sorted, it's time to organize the work system:
- Developing a consistent and easily searchable project folder structure.
- Standardizing templates for presentations, reports, or technical documents.
- Organize project schedules and task distribution using project management tools (e.g., ClickUp, Jira, Notion, or Odoo).
📁 Goal: All staff can find information quickly, avoid duplication, and accelerate cross-division collaboration (IT, BIM, Multimedia).

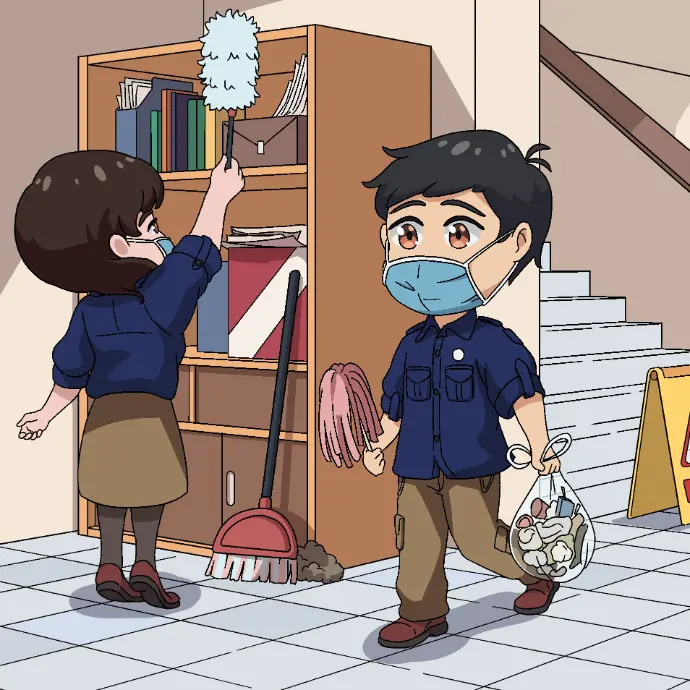
Seiso (Cleaning)
Digital Cleanliness and Physical Workspace
In the consulting world, cleanliness isn't just about the work desk, but also about digital cleanliness and the work environment:
- Clean your laptop of outdated files, cache, or burdensome applications.
- Ensure devices (laptops, tablets, cameras, drones, etc.) are in good condition.
- Maintain a tidy, comfortable, and representative workspace, especially when receiving clients or during hybrid meetings.
🧼 Goal: Enhance professionalism, maintain device performance, and foster work enthusiasm and comfort.
Seiketsu (Standardization)
Standardization of Consultant Work Practices
This stage emphasizes the importance of documentation and standard operating procedures (SOPs) to ensure consistent work quality:
- SOPs for data processing, BIM modeling, software debugging, or proposal submission.
- Digital document archiving guidelines.
- Checklists for client meetings, presentations, and project implementation stages.
📐 Objective: Maintain service quality, teamwork efficiency, and facilitate the integration of new staff or collaboration between divisions.
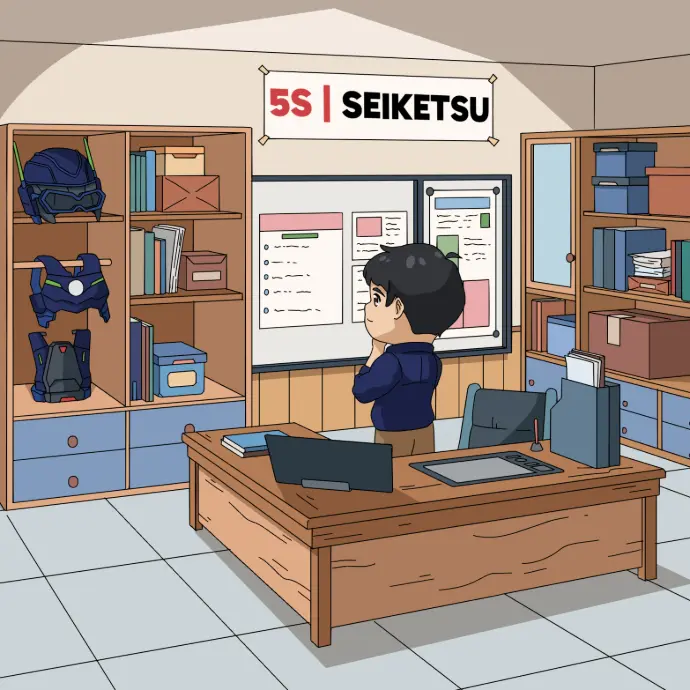
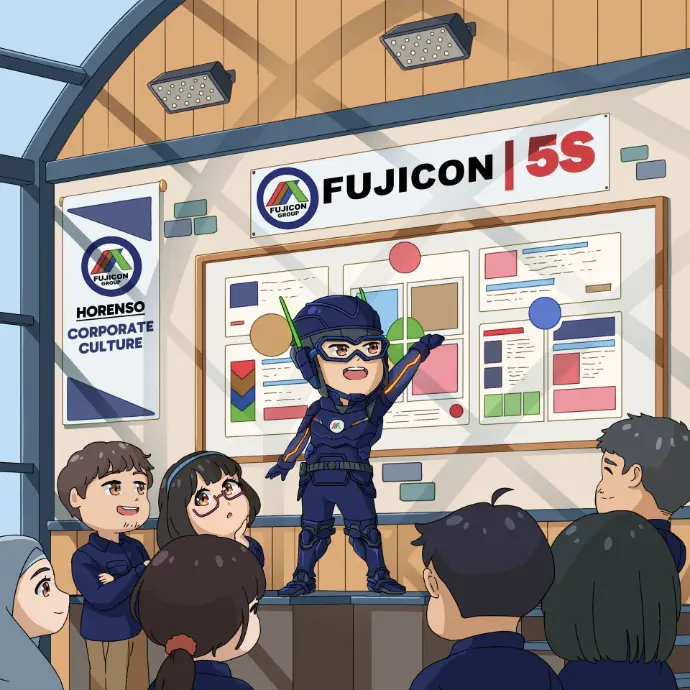
Shitsuke (Discipline)
Building an Orderly and Professional Work Culture
This is the most important phase: making 5S habits part of the company culture:
- Maintaining commitment to SOPs and project quality standards.
- Encouraging peer accountability among team members.
- Rewarding consistency and team contributions to efficiency.
🎯 Objective: Cultivating a professional culture that is disciplined, quality-conscious, and ready to consistently meet client demands.